Actual Copper Thicknesses (As Opposed to What You’ve Assumed)
Weight is still used as a determinant for copper thickness. Why?
Sometimes my columns tie to issues or stackups that appear in my inbox each week. I’m occasionally asked why 0.6 mils (15µm) is often used for the thickness of 0.5-oz. copper, rather than 0.7 mils (18µm), and similarly why 1.2 mils (30µm) is often used for 1-oz. copper instead of 1.4 mils (36µm). If you’re curious about the details, or if none of these numbers seems familiar, here’s a quick primer. The thickness parameter “t” in FIGURE 1 shows the thickness we’re interested in here.
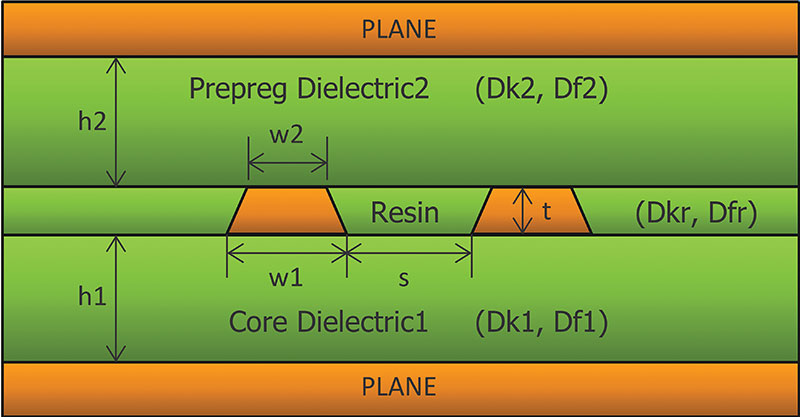
Let’s start the discussion with why weights (ounces) are used to describe thickness. If someone asked your height and you told them 180 lbs., they would think you were crazy. However, in electronics, weight is still used as a determinant for copper thickness. Why is that?
The ounce rating has its roots in the gold-foil industry and, subsequently, for copper’s use in the building industry. It’s based on spreading an ounce of a given metal over one square foot of area. Today’s copper foils for printed circuit boards are manufactured and sold by weight. The method has persisted for electronic circuits. There’s a good reason for it.
Nominal thickness. Thickness determination of rolled and electro-deposited (ED) copper foil by weight provides far more accuracy than contact-thickness gauges. Since the topography of treated foil varies greatly, and since the density of copper is known, weighing a 1 x 1 ft. sheet is the best way to determine the average thickness of a sheet of copper. So formally, the unit that we refer to as “ounces” is actually ounces per square foot. For example, 1-oz. copper weighs one ounce per square foot and is 0.00135″ or 34µm thick, nominally, as shown in TABLE 1. Some sources report the nominal thickness of 1-oz. copper at 35µm, but I’m using the IPC numbers rather than Wikipedia.
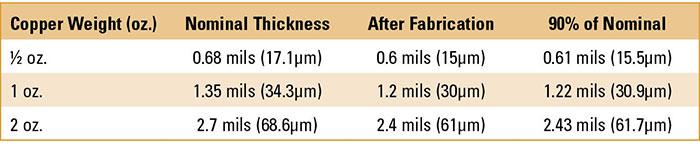
IPC-4562A. You may read other values for these nominal thicknesses from other sources, but manufacturers in the PCB industry are working from IPC-4562A, Metal Foil for Printed Board Applications.1 If your laminate or copper vendor provides different thicknesses, you may want to use this standard – or this column – as a guide for double-checking the numbers they provide. To this day, in fact, I see electronic design (EDA) tools using nominal thicknesses in their stackup representations, rather than the as-fabricated thicknesses.
The subject of copper weight and thickness becomes even more interesting when you factor in the tolerances described in IPC-4562A, which specifies the minimum thickness shall not be more than 10% below the nominal value in Table 1. If you’re a copper manufacturer pushing 2,000-5,000 tons of copper foil out per month, and you can keep your volume-production copper weights above 90% of the nominal values in Table 1, that’s a great way to save some money, and that’s in fact what happens in practice. The third column in Table 1 shows these 90% of nominal values, which are shown graphically for 1-oz. copper in FIGURE 2.
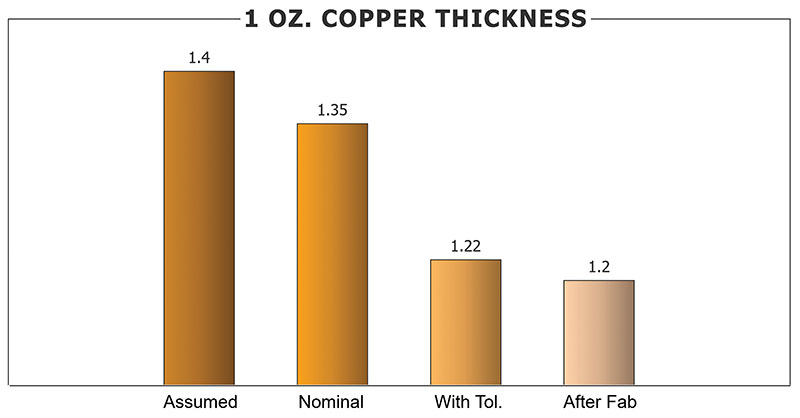
Post-fabrication. After fabrication, including etching and cleaning processes, the final thickness of these foils will average 0.2 mils (5µm) thinner than the “assumed” thickness (1.4 mils) for 1-oz. copper (Figure 2). Table 1 shows that 0.5-oz. copper will have a final thickness of about 0.6 mils (15μm). The fabricator may have an etching process that differs slightly from these values, but on 95% of the stackups I see from fabricators, these are the values used.
As a side note, the aluminum foil that most use for household cooking purposes is about 0.6 mils (15µm) thick, just like half-ounce copper.
Using inaccurate copper thicknesses. To calculate bulk resistivity from sheet resistance, sheet thickness is in the denominator, and whether you’re getting the thickness from an assumed or estimated thickness, as opposed to the weight-based methodology noted above, you need to understand the real values in PCBs, rather than values you might find on Wikipedia, for example.
I often see engineers, designers and EDA tools rounding the above nominal values to 0.7 mils (18µm), 1.4 mils (36µm), and 2.8 mils (71µm). I’m not normally against rounding, but when you’re rounding in the wrong direction, it needs to be questioned.
Board thickness, too, will be affected. On a four-layer design, the difference may not be significant, but on a 20-layer design using 1-oz. copper throughout and the wrong assumptions, the board thickness will be off by as much as 4 mils. I’m sure the mechanical engineers, if no one else, will appreciate if PCB designers worked with a sharper pencil.
FIGURE 3 shows impedance and skin effect loss at 10GHz for an 85Ω sample cross-section for 0.5-oz. copper using the post-fabrication number. Truth be told, the difference between a 0.7-mil thickness and the more-correct 0.6-mil thickness isn’t huge, but if you’re tracking millivolts and picoseconds, while signaling at multi-gigabit Serdes speeds and taking the time to simulate virtual prototypes using expensive signal-integrity software, it only makes sense to take every form of avoidable uncertainty off the table. Differential impedance will be affected. Signal integrity and crosstalk simulations will be affected. And losses from skin effect will be affected at some level. Why not feed that expensive SI simulator real numbers?
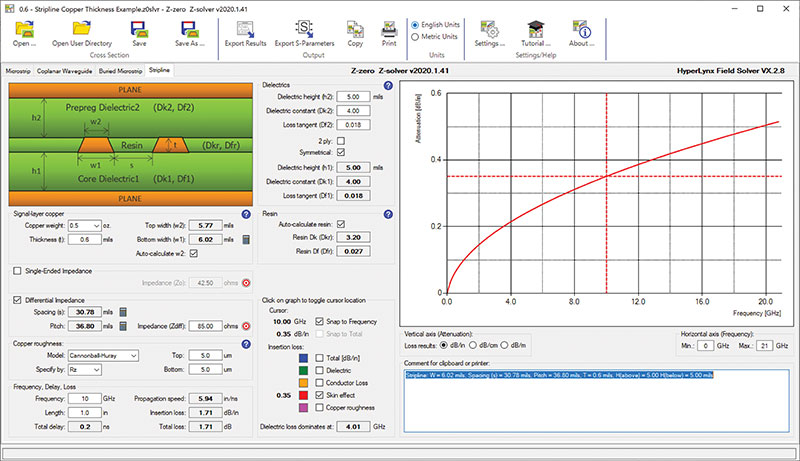
References
1. IPC-4562A, Metal Foil for Printed Board Applications, April 2008.